What are the Four Classes of Air Quality as per ANSI/ISA-71.04-2013 ?
Published : 06 Oct 2022
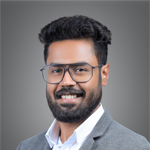
Author Name : Gifty Francis
The ANSI/ISA 71.04 -2013 is an international standard meant for creating conformity in the field of instrumentation. This standard covers airborne contaminants that affect industrial process measurements, control equipment, electronic office equipment, etc. The earlier version of the standard was published in 1985 and was reviewed in 2013 because of the reasons including the adaptation of lead-free regulation by the European Union (RoHS regulation) in 2003 and other countries in the following years. Lead was a highly corrosion-resistant element but was extremely detrimental to the environment. The lead-free regulation has made electronics more susceptible to corrosion than ever before.
The major changes in the 2013 edition included the use of silver reactivity as a metric for the determination of environmental classification. Provided definition of standard coupons and allowed real-time methods to be used for reactive monitoring based on which AQOZA has developed corrosion monitoring and control products.
This standard classifies the severity of the corrosive environment into different categories by the reactivity of silver and corrosion coupons. The infiltration of particles even in concentrations as low as parts per billion is sufficient to corrode electronics and therefore the reactivity of the silver and copper is measured in the unit of Angstrom (Å) which is one ten-billionth of a meter.
What are the different severity levels based on ANSI/ISA-71.04-2013?
Based on the different corrosive atmospheres the severity levels are classified as below:-
G1 Mild
Corrosion is not a factor in determining the equipment’s reliability. Corrosion is low that the reactivity on silver and copper is as follows:-
Copper reactivity : <300 Angstrom from an exposure of 30 days
Silver reactivity : <200 Angstrom from an exposure of 30 days.
Such a low severity level does not require any corrosion management measures as the corrosion rate does not possess any direct threat. G1 mild severity level is also an indicator of the effective functioning of the corrosion management system already employed.
G2- Moderate
Corrosion is evident and corrosion might be a factor in determining equipment’s reliability.
Copper reactivity: <1000 Angstrom from an exposure of 30 days
Silver reactivity: <1000 Angstrom from an exposure of 30 days
Quantifiable corrosion rates are always a threat to electronics. Effective corrosion management should be installed, and further offline monitoring of the corrosion rate is to be employed to check if the condition is worsening.
G3- Harsh
An environment where there is a higher risk of corrosion attacks and large failures of equipment.
Copper reactivity: <2000 Angstrom from an exposure of 30 days
Silver reactivity: <2000 Angstrom from an exposure of 30 days.
Large failure of equipment is imminent and needs a better corrosive management system. It is highly advised to use Corrosion control units with effective corrosion prevention methods. G3- Harsh Environment will need continuous monitoring of corrosion rate which can be achieved by online corrosion monitoring units.
GX- Severe
Equipment that is specially coated with a protective package will only survive in a GX- Severe environment. The probability of survival of equipment in this extreme severity level is slim to none. The manufacturer does not provide any warranty for their products as the lifespan is reduced to a great extent.
Copper reactivity: >2000 Angstrom from an exposure of 30 days
Silver reactivity: >2000 Angstrom from an exposure of 30 days.
Even though, there are solutions like protective coatings being applied against corrosion; but has limitation to cover entire parts of electrical and electronics goods, as there are parts which has to be exposed. The ideal solution to this corrosion for the indoor atmosphere is to remove the corrosion causing pollutant from the air. With a continuous monitoring and control of the corrosion within the facility will ensure the corrosion free environment for the equipment.
AQOZA technologies offer solutions to indoor corrosion monitoring and control. Our corrosion control units are standardized and designed to offer optimum economical solutions. Offline corrosion monitoring units can be employed for the initial corrosion survey which not only detects the corrosion reactivity but also identifies the corrosive gases after a surface analysis on the coupon surface at our facility. Our Online Corrosion monitoring units can offer real-time data on corrosion rates. Contact our experts now.