VOC Removal in Manufacturing and Paint Coating Industry
Published : 21 Apr 2021
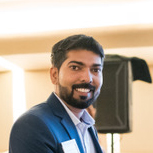
Author Name : Zahid, Co-founder & CEO
With several chemical compounds available on the earth, usually the term volatility is associated with carbon compounds known as organic compounds. In the category of organic compounds, a large number of organic compounds are volatile. These compounds include hydrocarbons, ethers, halo compounds, alcohols, esters and even acids. Volatility is a characteristic of small molecules. Some small inorganic molecules are
VOC emissions in Furniture & Paint coating:
In the furniture industry several mentioned above organic compounds come into use as solvents for the practices like polish, varnish, paints, glues etc. In addition, solvent applications have been widely used in paint & coating works, automotive paint booths in workshops, etc. These solvents must be volatile or of low boiling points. Otherwise, the drying process will take longer time and therefore it will will not be the suitable choice for the purpose.
In the process of manufacturing these products in order to reduce the cost of the product, manufacturers may use even harmful volatile materials that can cause severe suffocation, health & environmental hazards. In this category several nitrogen-containing compounds are also used. These solvents are likely to be cancer-causing compounds in nature. Moreover, there are low molecular weight materials said to be the most volatile with the size of less than 2 nano meters.
Thus, eradication of these VOCs from the industries is essentially the first and foremost breaking point.
How to remove low volatile VOCS?
Filtration units or adsorption media are curated based on the following parameters:
1. Stability of the filter.
2 Removal efficiency.
3. Disposability of the used filter material
4. Cost of the filter.
Activated carbon-based filters are known for such VOC removal applications. Since they add features like:
1. Environmentally friendly.
2. Highly efficient in adsorbing VOCs.
3. Economical & Stable.
4. Does not undergo any chemical reaction with the solvent material.
Moreover, when compared, the size of these organic molecules to the size of the pores of coconut carbon, is below 2 nm, which is appropriate. It is essential to check over the size accuracy, as the adsorbed material may escape from the filters if the pores are much bigger than the size of the solvent.
Coconut activated carbon filters are the right choice than coal & wood-based carbon filters, as in the case of coal or wood carbon, the pore diameters are much bigger than that of coconut carbon. Usually, disposal of such solvent filters after usage is a concern. But In the case of activated carbon filters, disposal is inexpensive and easy to handle, as it can be used as a fuel in many industries or used directly in metallurgy for the extraction of metals.
Learn Why is Coconut Activated Carbon preferred for Air & Odour purification?
To improve the efficiency of adsorption, activated carbons are impregnated with certain chemicals. It is highly possible that some of the solvents having distinguished acidic or basic characters, may escape the filter. In order to adsorb such vapours, activated carbon is impregnated with some transition metal salts that assists capability in absorbing both acidic and basic vapours.
In addition, we can impregnate oxidising chemicals in the activated carbon, which ensures continuous oxidisation to these low volatile vapours. Aqoza has developed various VOC removal activated carbons for various industries, which are highly efficient & effective in removing the VOCs along with disposable-friendly solutions. AQOZA has wide range of adsorption media for Odour control, Corrosion control and VOC removal applications.
For any further assistance and information, you may reach out to us via Contact us.